Hearing Aid Reliability and IP Ratings: Fact v. Fiction
Carolyn Smaka: Jenny and Torben, I look forward to picking your brain about hearing aid IP Ratings, and how audiologists should or should not be using those ratings in the hearing instrument selection process.
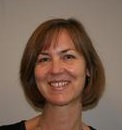
Jenny Groth: Thanks Carolyn. Everyone is interested in hearing aids that keep working throughout their lifetime – it is not in the interest of the patient, the audiologist or the manufacturer when they are sent in for repair. Audiologists want to recommend and dispense hearing aids that have long-term reliability, and patients want to know that they have made a sound investment.
It is now typical for manufacturers to advertise and market IP ratings for hearing aids, as if they are some kind of a quality indicator for long-term performance. There are a lot of misconceptions about IP ratings and what they really mean. They are not an indicator of longer-term reliability and performance. Manufacturers are making a great deal of effort to use different technologies in ways that will ensure that the hearing aid keeps working reliably, however. We are also doing a lot of qualification testing that is much more significant to long-term reliability than what is covered by the IP test.
Carolyn: Before getting into the misconceptions, let’s start with the IP ratings themselves. What exactly are IP ratings, and why are they not an indicator of long-term performance?
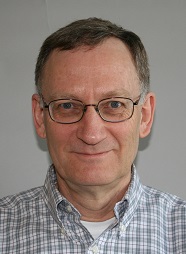
Torben Groth: The IP rating was originally developed for testing electrical equipment under very adverse conditions. These types of equipment can have high voltages, and you also want to ensure the safety of people working in or around this equipment.
IP stands for Ingress Protection, and the rating classifies the degree of protection provided against the intrusion of things like dust, water, etc. The first digit after the IP is for solid foreign matter – it rates the equipment or device for protection against solid matter getting inside. Solid matter could be dust, or fingers for example. You can imagine why it would be important to know if someone’s hands or fingers could get inside a piece of electrical equipment, or into an electrical socket. As the number gets higher, it means that that the solid particle is getting finer.
For example, a level 2 rating would be protection against a finger or similar object getting inside, while a 5 or 6 is for dust. With a 5 rating, some dust is allowed to get inside the device during the test, but it must not affect the performance of the device. A 6 rating means there is no dust ingress at all.
The second digit refers to the level of protection that the equipment or device provides against the ingress of clean water. The criteria take into account various ways water can be introduced into the device, such as trickling, hosing, immersion, etc. The common denominator here is that the water should not affect the working of the device at all.
For example, an electrical socket rated IP22 is protected against insertion of fingers and will not be damaged or become unsafe during a specified test in which it is exposed to vertically or nearly vertically dripping water.
Carolyn: So, you expose the device to these tests, and ensure they continue to work?
Torben: Correct. The device should continue to work when you expose it to these tests. That is one of the main problems when using this standard for hearing instruments.
Consider an IP 57 rating for example, where the 7 indicates that you take the hearing instrument and immerse it in water to a depth of 1 meter for 30 minutes. As you know, when you immerse a hearing instrument in water it quits working within a few minutes because you suffocate the zinc air battery. Are you actually then testing according to the intent of the standard?
Jenny: One thing we should also point out is that independent labs conduct the testing and you do not actually get a rating. You decide in advance that you want the laboratory to test for a particular rating, such as IP 57 or an IP 68 and then the lab carries out only that test. It is not that they start at 00 and work their way up until there is a failure.
In addition, you may see claims that a manufacturer or product is “certified” at a certain IP rating. In fact, there is no certification process. After your device has been tested, you receive a report on how your device performed under the test conditions. You, as the manufacturer, decide if you are satisfied with the way your device performed under the test that you ordered.
Carolyn: If the IP rating was developed for electrical equipment and we are not really testing hearing aids according to the original intent of the standard, how did the IP ratings make their way to our industry?
Torben: One company brought a hearing aid to the market that was completely watertight. They were in need of some kind of testing standard to actually prove their design goals. There is no test in our industry that will qualify a hearing aid design for this so they looked at the International International Electrotechnical Commission (IEC) standards and found standard 60529, which deals with electrical equipment but has a number of tests that could prove their design. The hearing instrument was tested to an IP rating of 68, with 6 indicating that there was no dust inside the hearing instrument at all, and the 8 indicating that there was no water inside the hearing instrument after immersion beyond 1 meter for an extended period of time.
That is where it all started, and soon after, every manufacturer started taking their existing designs and testing them according to these IP test codes.
Carolyn: When Jenny indicated that IP test is not a test of long-term reliability, this makes sense. Just because no dust or water may have entered the instrument during this test, doesn’t mean that the instrument will not stop working for whatever reason at any time after the test. We know there are many reasons for hearing aid malfunction.
Jenny: The appropriateness of the test is a really important point. What does that really tell you about what the hearing aid is going to do over a longer period of time?
Torben: IP rating is not predictable of long-term reliability. It also does not relate to what I would call a hearing instrument real-life use scenario. For example, the test specifies the use of clean water. If you expose a hearing instrument to clean water, probably nothing will happen. But if you take it to a swimming pool with chlorinated water or on a boat where you have a salt water spray, that is a different story.
It is a myth that the highest number on an IP rating gives better protection. That is not the case. These are individual tests. It is not a degree of protection that you get by adding to the number itself.
Carolyn: What kinds of things do affect long-term reliability? How should we be counseling our patients to do to get the most out of their hearing instruments in terms of long-term reliability?
Jenny: The things that we have always been counseling about still hold true today.
Good advice for care of hearing aids includes obvious tips such as, try to keep the hearing aids as clean as possible. Use the cleaning tools provided by the manufacturer to brush off the openings for the microphone and the receiver, and use a soft cloth to wipe them off whenever you take them out. Keep the hearing aids dry and use a dry aid kit to store the aids in when not in use. Make sure that the hearing aids are well protected when you are not wearing them, try not to drop them, and do not leave the batteries in them for extended periods when the aids are not in use.
Torben: We know that things happen – you may get stuck in a rain shower while you are wearing your hearing aids, or forget to remove them when getting in the shower. If this should occur, take the battery out, dry the aids with a soft cloth and leave them open to fully dry out, or use a drying kit if you have one. When it’s completely dry, insert a fresh battery and you may find the aid working again. We design the hearing aids for real world use, including occasional accidents. Testing according to the IP system does provide a snapshot of whether a hearing aid is likely to survive such an accident, and ReSound includes testing to the IP57 standard in our battery of environmental tests. Similar to what other manufacturers report, test results have been that the devices continue to work once the battery is replaced.
Carolyn: I have heard a bag of rice can help dry out an iPhone that has gotten wet, although I’m not sure if that works or is a wives’ tale. Would that work with hearing aids that have accidentally gotten wet?
Jenny: The idea is to dry the hearing aid out if it gets wet. Rice might work as it absorbs moisture, but just opening up the hearing instrument, removing the battery and letting it dry out is fine. Or using a dry aid or dry and store if one is available.
Carolyn: What steps have manufacturers taken to address long-term reliability?
Torben: We use a number of techniques. We start by looking at the areas on the hearing aid where contaminants could enter and have a detrimental effect. We apply glob top, which is an epoxy coating that will shield the hearing aid’s integrated circuit. We protect the contacts and battery springs as well. At ReSound, we also use nano coating on every part of the hearing aid inside and out. Nano coating changes the properties of the surface in such a way, that if a vapor condensates on it or liquid gets in, it will bead up and roll away.
A tray of finished hearing instruments is loaded into a vacuum chamber where they will be nanocoated.
Carolyn: Do we have any studies to show that nano coated instruments are getting better long-term performance or have less repairs due to moisture?
Torben: Yes - we run what we call an AST or accelerated screen testing, which is a number of standardized tests that should emulate real life conditions. We use this testing to try and predict what the effects would be over a three to five year period. We test both nano coated and non-nanocoated devices, and the test data show that nano coating significantly reduces the need for service and repair.
Close up view of the microphone filters of two hearing aids after undergoing the AST test. This photo illustrates how a non-nanocoated hearing aid (left) is more likely to accumulate debris such as cerumen than one that has been nanocoated (right).
Nano coating helps with protection against moisture, sediments and to some degree with wax, in that it may help delay a repair for wax build up. Also, if you nano coat the screens and filters for the entry openings into the transducers, you will see a slower build-up of particulates and wax that may result from daily use. There are a lot of advantages to nano coating and ReSound is, at least to our knowledge, the only manufacturer that protects the entire hearing instrument under a vacuum condition, so the nano coat polymer enters every nook and cranny. We use nano coating as the final process after assembly so the entire instrument including hooks, receivers and all are nano coated. I think that sets it apart from the rest of the industry because they use a lot of partial coating, where some parts are nano coated and others are not.
Carolyn: One message today is that professionals should not use or interpret the IP ratings as way to gauge product reliability. How then do we select products with the best long-term reliability for our patients? It seems like we need to go by our experience, e.g., I had a lot of device failures for manufacturer A, so I switched to manufacturer B and have not had any problems.
Jenny: That is a good question and I think this is why people are asking for IP ratings. They want to be able to quantify reliability.
No manufacturer is doing accelerated environmental testing against other manufacturers’ products. No one has the data to support that they are the best on the market in terms of how robust their products are. As the professional, you are in the best position to compare products based on your experience, and keeping in mind all the many variables that contribute to long term performance including care and use, etc.
Torben: Our industry lacks a common standard for how to test hearing instruments when it comes to environmental protection. That is really what we need. Then we can start comparing manufacturer to manufacturer. Today you see claims like “ours is the best”, “we have the best nano coating”, and “I have a higher IP rating than you do”. But these claims do not really say anything about product quality.
Carolyn: This has been very informative! Thanks Torben and Jenny for a great discussion.
For more information about ReSound, visit www.gnresound.com or the ReSound Expo Page on AudiologyOnline.